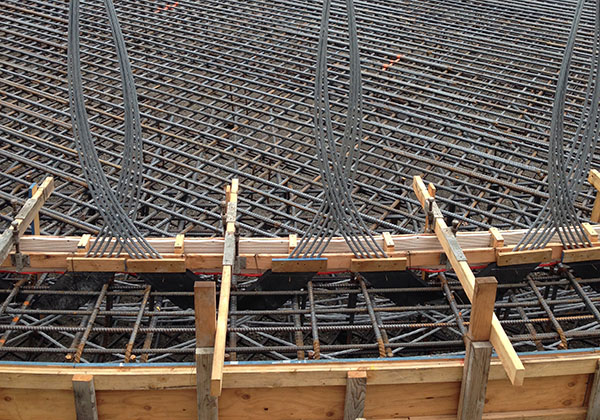
Building a Critical Piece of Infrastructure Adjacent to the San Andreas Fault
West Yost provided design and support during construction for a 2.0 MG prestressed concrete tank with a dome roof to replace a 60-year old concrete tank. The project site is located within 300 feet of the San Andreas Fault and sits between two faults just north and east of the tank. This tank is a critical component in the City’s day-to-day operation of its water supply system and provides emergency fire storage. During off-peak water usage this tank receives water from tank in a lower pressure zone and also pumps water to another tank in the next higher pressure zone; thereby, filling all the City’s water storage tanks during the off-peak periods. Then during periods of peak water usage water flows, by gravity, from tanks located in upper pressure zones to the lower pressure zones. Consequently, each tank is a key component in providing water to the City’s residents.
The original tank was a prestressed concrete structure built in 1950, and due to seismic and structural deficiencies the City had been operating the tank at 50 percent of its total capacity creating a water storage shortfall in the system. Consequently, the City’s primary goals were to enhance seismic survivability with low maintenance sustainable infrastructure. Performance of this tank is mission critical as it serves as the lifeline structure for fire flow, daily demand, and is vital to the local economy.
The Glenview Tank 3 is situated within a few hundred feet of the active San Andreas Fault, which posed unique geotechnical and structural challenges to the City and project designers. The tank sits between the surface rupture zone of the 1906 Great San Francisco Earthquake (280 feet west), and the Pampeyan fault trace (180 feet east). Observations made in 1908 indicated that a fence line near the current tank site was deformed by 1906 fault rupture. The post-earthquake fence alignment suggested about 7 feet of fault displacement abruptly occurred along the main San Andreas Fault trace.
Given the geologic evidence and observations following the 1906 event, it was concluded that similar distributed ground deformations are possible due to a future rupture of the adjacent active San Andreas Fault trace. This ground deformation may cause abrupt surface offset, differential settlement, tensile stress due to ground elongation, and tensile cracking of the ground. The following measures were implemented into the tank design in order to mitigate these potential effects.
- The tank is supported on engineered fill reinforced with several layers of geogrid. The reinforced fill is designed to enhance ductile behavior, which serves to partially decouple horizontal deformations from the foundation and mute vertical deformations.
- The tank is supported on a mat foundation designed to resist planer racking due to differential horizontal displacement and span/cantilever unsupported areas due to vertical ground deformation. The foundation is 30 inches thick with a total of 254,150 lbs of reinforcing steel and 900 cubic yards of concrete.
- Seismic shutoff valves, flexible pipe connections, and a secondary earthen containment berm around the perimeter of the tank were also implemented.
An AWWA D110 Type I tank was specified for the Tank 3 Project and designed with an anchored flexible base connection between the foundation and the wall. This “base isolation” style detailing reduces bending moments induced by hydrostatic, thermal, and seismic forces as the tank wall is separated or “isolated” from the wall footing by a neoprene bearing pad. Base isolation enhances operational and seismic performance of the tank by allowing the floor and wall to act independently of each other. Similar detailing is now used in critical buildings, such as hospitals, to help ensure survivability during earthquakes.
In areas of high seismicity the sloshing wave is also critical to the design of liquid storage structure. For the San Bruno project the calculated sloshing wave, per ASCE 7-10, is 12 feet. A cast-in-place free span concrete dome roof was used to accommodate the seismic forces and the sloshing wave. Through structural design modifications to the concrete dome roof and prestressed concrete tank wall, the freeboard was reduced to 6’-3”.
The Project also included mechanical design for tank and associated pipes and valves, grading plan, chloramine chemical feed system, tank mixer, and site security improvements.
Team Spotlight
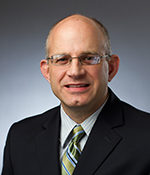
Jeff Wanlass, PE
Principal Engineer II
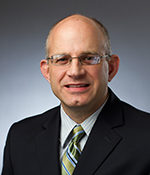
Jeff Wanlass, PE
Principal Engineer II
“I got into this career because I liked figuring out how things work. My dad encouraged me toward civil engineering. I enjoy both the planning and design. In my early career I focused on planning and analysis and transitioned into a design focus. I like resolving critical issues with design and helping clients resolve current operational issues to develop a solution that resolves both their current and future needs.
I enjoy working at West Yost because the people I work with are all excellent and driven by similar goals as I have to help clients meet future needs. A project I’m proud of is the City of San Bruno Glenview Water Storage Tank 3 Project. It is located within 300 feet of the active San Andreas fault trace. In fact, there is a fence on that site that shifted six feet in the 1906 earthquake! It was a fun project because we were able to work collaboratively with city staff, the tank builder, and the geotechnical and structural engineers to develop mitigation measures so that the tank would still be operational after an earthquake. I am proud that it was presented at two AWWA conferences and was featured in Source magazine.”
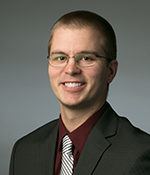
Scott Greenwood, PE
Associate Engineer I
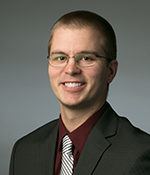
Scott Greenwood, PE
Associate Engineer I
“I look forward most in my work to the unknown on a daily basis. The work and change can range from helping with water projects, sewer projects, rehabilitations, cost estimating, project management. The biggest thing I get excited about is being able to work on something new every day as with a support team around me in the event that i I have any questions that need answering, it leaves the door open for learning new things!
My biggest accomplishment was the design package together for the large scale Hayward recycled water project, I was able to go through the design, provide a high quality work product, and I a have billed over 2,000 hours to that project. We ended it on time, it had 85 design sheets and was a very large package. It was very well received. It gave the city the ability to get recycled water to new customers on a large scale, and I’m proud of that.”